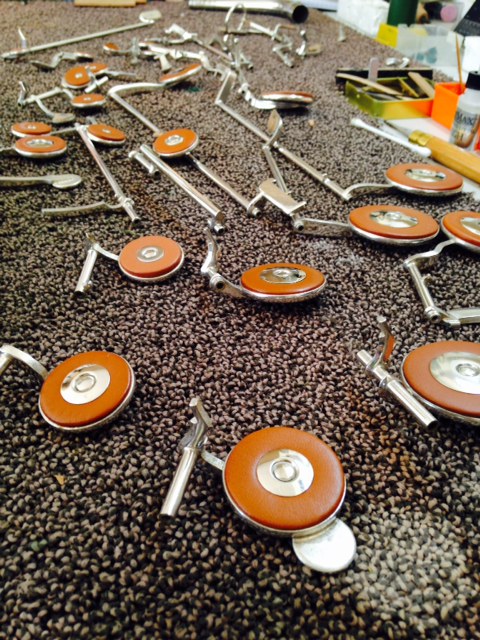
Don’t hesitate to contact me via the contact page of this website or via email at info@safesax.nl
You can always visit me in my workshop in Maasbracht, the Netherlands (by appointment only)
Please call +31 6 31555931
As a saxophone repairman I take complete responsibility for your beloved instrument. I care about doing things the right way, and fixing things so they do not need to be fixed again. When I overhaul your saxophone, your horn will be 100%, and you will experience what it is like to have a horn that wants to make music.
The longevity of the padwork, on the depth of my understanding of the mechanics and acoustics of the instrument are most important to me. With honesty and openness, I freely share the knowledge with you throughout the process of overhauling your horn. I take however much time it needs and expend however much effort it takes to make your horn the best it has ever been. I do everything myself, and my hands are the only hands on your horn from start to finish.
My overhauls typically represent between 10 (student instruments) and 32 (pro instruments) hours of labor – not including many hours of playtesting. There are no shortcuts when you want it done right, when you want things fixed that have been overlooked not only from previous repairmen but from the factory itself.
You will get complete access to my workshop and you will have all the freedom and time to playtest your instrument as long as you like.
Every instrument has it’s own character just like every musician
Depending on how much you play, you can expect your pads to seal and feel well for 5-10 years. The low end of the estimate is for those who play 5+ hours a day. If you only play an hour a day, you will probably get 10+ years out of the pad job.
You will (possibly for the first time) understand what a saxophone can feel like when it is done right. Low Bb is just as easy as any other note, altissimo pops out because even your secondary adjustments actually work and seal properly, you can play as loud or as soft or as hard or as easy as you want and you no longer think about the saxophone as something you have to wrestle to get your way- you just listen to the music you are making. Your standards will go up, you will start to see how much unrealized potential lays inside most saxophones, and you will never be able to go back to playing a saxophone that isn’t the way it is supposed to be.
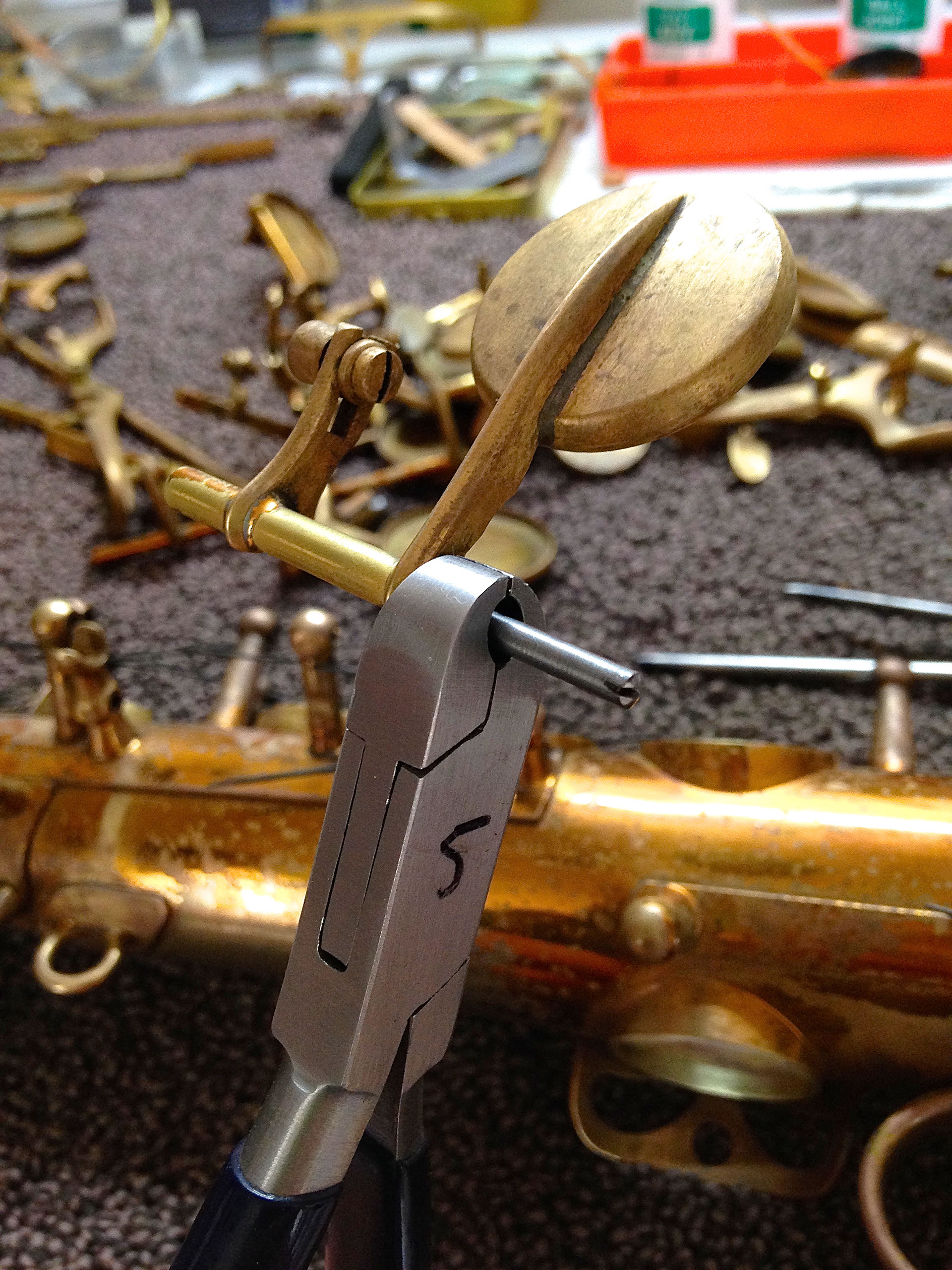
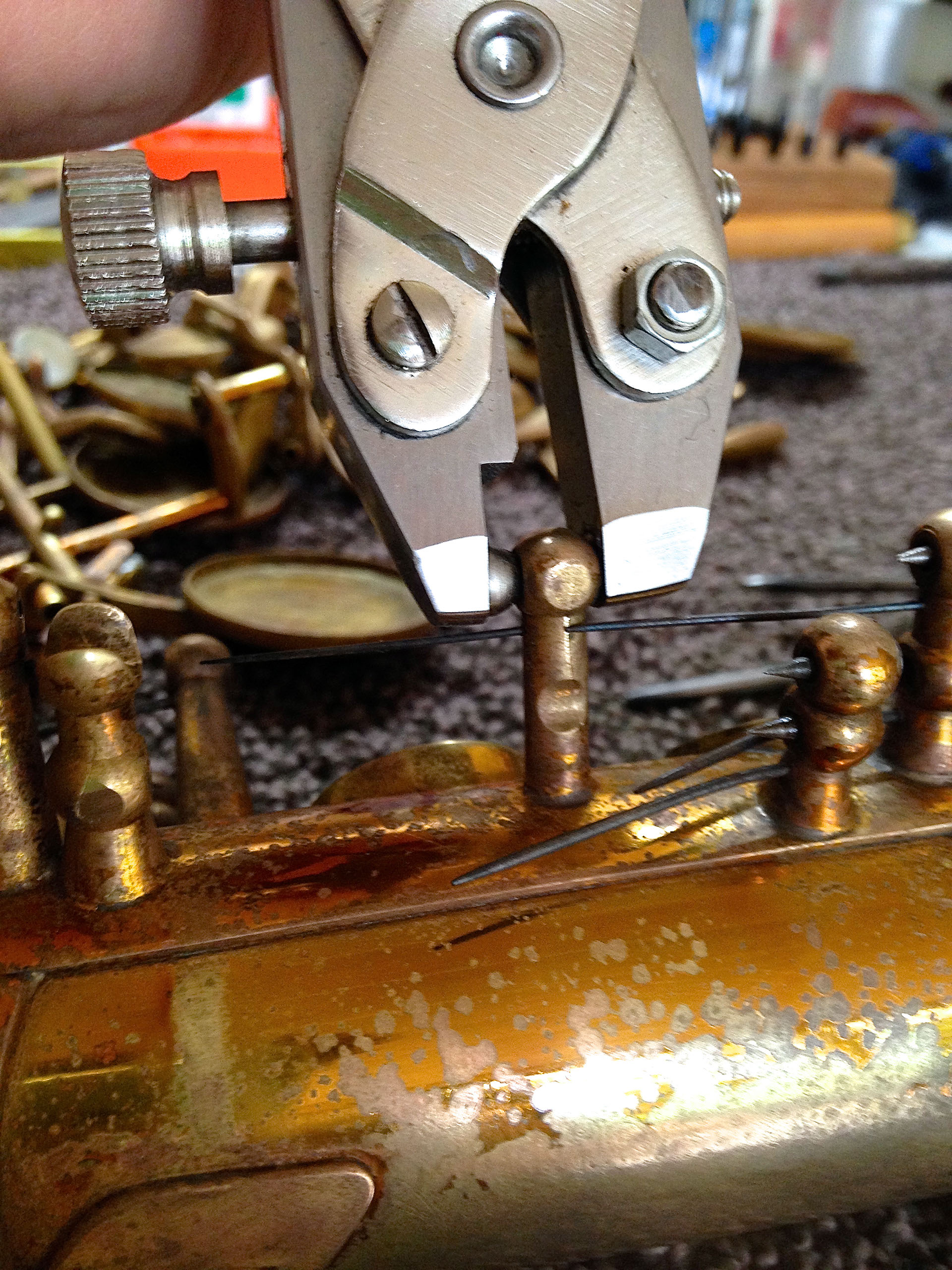
REPAIR PROCEDURES -GENERAL MAINTENANCE
(costs between €150,- and €300,-)
- Inspection of the instrument and it’s case
- Complete disassembly
- Clean and degrease of all parts
- Checking all the soldering
- Polishing of silver plated instruments by hand (this is the only right way to not deform keywork and tone holes and the silver layer will last longer!)
- Remove dents and straightening of body
- Checking neck tenon and receiver. They are made to fit perfectly smooth and airtight. Usually this involves correcting asymmetry, gently enlarging the tenon, and then lapping the tenon and receiver for perfect fit. The neck tenon leak is unfortunately an extremely common problem, and the whole horn will suffer. When you play a “dead” horn, often correcting a leak at the neck tenon joint will bring it back to life.
- Replace worn out pads, corks, felts, teflons and springs
- Assemble the sax step by step and adjust every corresponding key
- While assembling all the rods get new high quality oil and the pivot screws special grease. All kinds of little imperfections get fixed as well as placing crescents to solve intonation problems and much more…
Something to think about: old oil causes the keywork to wear out very fast because the oil will transform into an abrasive! On the other hand,
too much oil on the keys attracts dust, giving the same results.
Your saxophone will stand head and shoulders above other new saxophones of the same make and model and will feel and play the best it possibly can.
(6 months warranty on general maintenance. Safe Sax does not provide warranty on defects caused by external influences or materials which have not been caused by a Safe Sax maintenance.)
REPAIR PROCEDURES – THE OVERHAUL
Each overhaul is different, and tailored specifically to the needs of your particular saxophone. I have listed some of the more common procedures I employ below. My overhaul will ALWAYS include the following:
- INSPECTION OF THE INSTRUMENT AND IT’S CASE
Making notes of visual defaults like deformed body, neck, keys. Measuring key heights. Check if the sax has good protection in it’s case.
- DISASSEMBLY AND CLEANING
A complete disassembly of the instrument followed by a thorough degreasing of the body and keys, with a gentle handwashing of the instrument. If the horn has excessive corrosion, this can be followed by a special chemical dip designed specifically for instrument work to remove corrosion without affecting lacquer or plating. After being dipped, the instrument is rinsed and carefully handwashed again, followed by a hand-drying followed by pressurized air to remove any leftover liquids from the nooks and crannies. Any key rods/pivot screws are carefully degreased to remove any corrosion from the steel. Hinge tubes, pivot receivers, and all posts are hand cleaned to remove years of grease. grime and dried oil buildup.
- DENTWORK AND STRAIGHTENING OF BODY
The saxophone is checked for straightness, correct alignment of the neck and bell relative to the body, dents or malformations affecting the levelness of toneholes, and dents and dings and past dentwork that could be improved. Minor dents and straightening of the body (which is more common than you would expect) are included in the overhaul. Major dentwork will be estimated on a case-by-case basis.
- LEVELING TONEHOLES
Carefully leveling toneholes to be perfectly flat, thus ensuring a long-lasting pad seal. Saxophones never come out of the factory with truly level toneholes, and if they have been relacquered or otherwise damaged in the past, it is highly likely that the toneholes are quite unlevel. This work is done by hand with specially designed tonehole files (although they might more accurately be called burnishers for how slowly they work) and is never done without careful consideration of how best to preserve the instrument for its future. Barring any future damage, this should not need done again. This can only be done if all pads are being replaced.
This has no consequences for intonation.
Sharp tonehole edges cause the pads to stick and wear out fast. So after leveling they will get a smoothening treatement.
- ALIGNMENT OF POSTS
Every post is aligned straight and true. Depending on initial build quality and past damage (or repair work) this can include bushing and/or carefully resoldering the post in the correct location.
- STRAIGHTENING OF ALL RODS
Every rod is made straight and true, cleaned and polished smooth. If necessary the rod is replaced.
- PIVOT SCREWS AND PIVOT RECEIVERS
Screws and receivers will be cleaned and checked for symmetry and perfect fit. Necessary adjustments will be made to correct misshapen screws (OEM replacements if available, repair or fabrication otherwise) and pivot receivers are remade and reamed with a specialized exact-shape reamer.
- ALIGNMENT AND LEVELING OF KEYCUPS
All keycups are aligned perfectly with their respective toneholes and each keycup is leveled and reformed as necessary for perfect pad fit.
- ADJUSTMENT OF ALL SPRINGS
All springs are checked and tensioned in the correct alignment and attitude for snappy feel under the fingers. Worn or damaged springs are replaced.
- REPLACING ALL PADS
As standard I use airtight CHANU, RIGOTTI deluxe and PISONI PRO pads with metal resonators (Selmer style). These pads give always the best result for a lot of players.
These pads let all the natural quality of every saxophone florish.
Of course I’m open to personal preferences.
Pads or glued with warm synthetic glue. They are seated with the spring engaged and pressure applied as it will be during usage- with each pad tested for absolute perfection of seal in all possible playing conditions. The pad seat is as shallow as is possible, with the pad sealing firmly and evenly all around at the same exact moment for that satisfying drumlike pop. No clamps are EVER used in seating. With such a shallow seat, as you play the pad will conform itself to your personal playing pressure, and with good care you can expect your pads to last for 5-10 years before leaks appear, even playing for hours a day.
- OILING
All hinge tubes are assembled with super high-quality key oil with the excess wiped off so as not to attract dust. Pivot screws and rollers are assembled with special high-quality grease designed specifically for saxophone pivot screws. The synthetically based oil and grease I use is especially designed to not break down or thicken over time.
- REPLACING ALL FELTS/CORKS/TEFLONS
Replacing every single adjustment and silencing material on the instrument. I use a combination of many different synthetic materials in addition to natural cork and felt, and how I set up each instrument is determined by what I believe will work best for that particular horn. Extreme attention is given to longevity of the adjustment, quietness of the action, and slick movement of parts.
- NECK TENON FIT
Neck tenon and receiver are made to fit perfectly smooth and airtight. Usually this involves correcting asymmetry, gently enlarging the tenon, and then lapping the tenon and receiver for perfect fit. The neck tenon leak is unfortunately an extremely common problem, and the whole horn will suffer. When you play a “dead” horn, often correcting a leak at the neck tenon joint will bring it back to life.
- THE LITTLE THINGS
Each horn is unique, and if I were to list all of the things I check and correct if necessary, this section would be a novel. I check every little thing on your horn- from the spring receivers being the right shape for correct function to the threads in the posts being absolutely clean, from the roller rods being free of corrosion to the keyguards being straight. Old solder job done sloppily? Safe Sax will redo it to be correct. If its not right, its not done.
- INTENSIVE PLAYTESTING AND ADJUSTMENT
Once the work is complete, I spend a few days playing, tweaking, and adjusting the horn as it settles in. This is where I will notice the tiny things that one can only notice by living with an instrument, and makes sure that each and every job I do is personalized and made the best it can be. This work is essential, cannot be rushed, and makes the difference between an average repair and a horn that you never argue with.
The following procedures may or may not be needed to varying degrees on your horn:
- DENTWORK AND SOLDERING This is done in a bespoke fashion- that is, it is different and unique to each instrument that needs it. This work is priced, discussed, and decided upon ONLY by having the instrument in-hand.
- HAND POLISHING OF PLATED FINISH A careful, painstaking and conscientious cleaning and hand-polishing of plated finishes that removes all tarnish and scale and brings however much plating remains on the horn to near-new condition.
- MECHANICAL RECONSTRUCTION OF THE KEYWORK (only for the Pro/Vintage overhaul) A restoration of the keywork to better-than-new mechanical condition. When this work is completed, your keywork is as smooth and as silent as it can possibly be. ALL play is removed from the hinge tubes and pivot rods. Hinge tubes are gently swedged tight using collets, with regard to the integrity of the finish, and then made square and true with hinge tube facers so that the bearing surfaces of the ends of the hinge tubes are perfectly flat, thus ensuring a long-lasting and smooth fit. All posts are faced flat and swedged tight around the rod. The pivot screw bearing surfaces are checked and if the screw is uneven, it is replaced with an original replacement part. The pivot receivers on the pivot rods are thoroughly cleaned out, checked, and perfected to match the pivot screw exactly. Then the pivot screw post is counterbored until the pivot screw and pivot rod fit perfectly, being absolutely free with no play. This can only be done if the related pads and adjustment materials are being replaced, and should be done in conjunction with a chemical cleaning, tonehole leveling, and pad/felt/cork/teflon replacement. This is the service to get if you want your horn to be as perfect as I can possibly make it and better than it was when it left the factory.
CLICK HERE for videos about the mechanical overhaul on my YouTube channel.
WARRANTY
All repairs come with a one year warranty on pads and materials and a five year warranty on mechanical work. When the saxophone owner did not treat his horn in a gentle way or its case is not in good condition Safe Sax will not honor the previous warranty.